Pablo schaut durch seine Techno-Brille. Er sieht alles, wie sonst auch, wenn auch wir ihm mit bunten Kreisen und Pfeilen auf Dinge hinweisen, wo er noch einmal genauer hinschauen muss. Es ist heiß in Mexiko. Trotz der hohen Temperaturen ist Pablo gut ausgestattet mit seiner persönlichen Schutzausrüstung. Es ist früher Morgen, als er sich die Brille aufsetzt, mit der wir in Bremen sehen, was er sieht.
Pablo ist ein Mitarbeiter eines großen Zulieferers für Automobilteile. Die Firma hat sich schon vor einiger Zeit auf Produkte für Elektroautos spezialisiert. Jetzt, während der Corona-Krise ist der Produktionseinbruch zwar deutlich spürbar, aber sie läuft weiter, wenn auch auf Sparflamme. Entlassungen gab es bisher noch keine und das sollte auch so bleiben, hat die Unternehmensführung beschlossen. Es war geplant, dass wir uns die Produktionsanlagen ansehen sollen und diese auf Sicherheitsmängel hin überprüfen. Zwei Wochen vor Ort waren veranschlagt, derzeit unvorstellbar. Hotels, Restaurants und vieles mehr haben geschlossen. Von Flügen aus Europa mal ganz abgesehen.
Wir waren schon mehrmals vor Ort, aber sind noch lange nicht fertig mit der Begutachtung der Produktionsanlagen. Hunderte, teils selbst gebaute oder oftmals umgebaute Maschinen warten noch auf das geschulte Auge. Unser Auftraggeber hat leider mit einer mehr oder weniger stagnierenden und recht hohen Zahl von Unfällen zu kämpfen. Diese zu verringern ist das Ziel. Gründe gibt es viele. Von falschem Verhalten über mangelnde Sicherheitstechnik bis hin zu Manipulationen von Schutzeinrichtungen. Vieles haben wir bei den letzten Besuchen zu Tage befördert und so manchem die Augen geöffnet. Diesen angestoßenen Prozess wollen alle, trotz Corona nicht unterbrechen. Die Unfallzahlen belegen bereits, dass wir den richtigen Weg eingeschlagen haben. Sie sinken.
„Stopp!“ sage ich, während Pablo eine Lücke in einer festen trennenden Schutzeinrichtung im Blick hat. „Miss bitte einmal das Öffnungsmaß mit dem Maßband und den Abstand zum Greifer des Roboters, wenn er das Bauteil ablegt.“ Damit er weiß, was genau er messen soll, malen wir ihm einige Hilfslinien ins Blickfeld. Als er das Maßband anlegt, machen wir Screenshots. Zudem wird die Inspektion aufgezeichnet, falls uns später bei der Erstellung der Risikobeurteilung doch noch Details fehlen.
Trotz Tausender Kilometer zwischen uns sind wir in der Lage, zeitgleich dieselben Dinge zu sehen. Wir liefern Hilfestellungen, erläutern warum es genau auf dies Detail ankommt, und helfen so, den Blick zu schärfen. Nach gut vier Stunden sind die Akkus leer. Die von Pablo und die der Brille. Wir telefonieren noch, welche Maschine als Nächstes dran ist. Pablo schickt uns ein Layout, ein paar Fotos, damit wir uns besser vorbereiten können. Schaltpläne und Funktionsbeschreibung erhalten wir per E-Mail. Wir sichten noch einmal die Daten der heute begutachteten Maschine, machen uns Notizen und dann Feierabend.
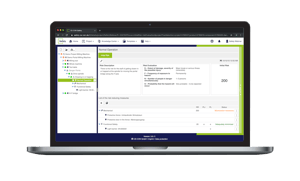
Die gefährlichsten Stellen haben wir direkt in unserer Cloud-Software CE-CON Safety dokumentiert und mit notwendigen Risiko mindernden Maßnahmen versehen. Wir sind sicher, dass morgen, wenn wir die nächste Maschine ansehen werden, bereits ein Teil davon fertig sein wird. Schließlich hat Pablos Team auch Zugriff auf die Software. Beschreibungen sind stets bebildert. Bilder, an die sich Pablo sehr gut erinnert. Schließlich hat er es mit eigenen Augen gesehen.
Schon vor Corona haben wir begonnen, unsere Kunde aus der Ferne mittels Augmented-Reality zu unterstützen. Die anfängliche Skepsis, ob es sich lohnen würde, eine teure Brille zu kaufen, war schnell verflogen. Mitarbeiter werden gleichzeitig geschult, Prozesse beschleunigt und obendrein ist ein Aufenthalt mit Jetlag, Flügen, Mietwagen, Spesen und Hotels in fernen Ländern um ein vielfaches teurer als eine Augmented-Reality-Brille.
Sie interessieren Sich für Arbeits- und Maschinensicherheit und wollen über aktuelle Themenaus diesem Bereich informiert werden? Dann abonnieren Sie jetzt den CE-CON Newsletter!