In Betriebsanleitungen ist das Kapitel „Instandhaltung“ fester Bestandteil. Bei umfangreichen regelmäßigen Arbeiten wird der Maschine häufig sogar eine eigene Instandhaltungsanleitung beigelegt. In wöchentlichen Abständen müssen gemäß Wartungsplan Komponenten geschmiert oder geprüft werden. Potentielle Unfallgefahr, besonders, wenn sich diese Komponenten im Sicherheitsbereich befinden und Schutzeinrichtungen wie Umhausungen außer Kraft gesetzt werden müssen. Doch Instandhaltung geht auch sicher – wenn Hersteller und Betreiber die folgenden 5 goldenen Regeln beachten und verzahnt zusammenarbeiten:
1. Die Gefährdungsbeurteilung
Der Betreiber einer Maschine hat gemäß Betriebssicherheitsverordnung die Verpflichtung, regelmäßig und anlassbezogen eine Gefährdungsbeurteilung an jedem Arbeitsplatz durchzuführen. Wie der Satz schon erklärt, darf die Beurteilung nicht bei dem Normalbetrieb enden. Führt der Bediener die Instandhaltung selber durch, so muss der Betreiber prüfen, ob er zum Beispiel ausreichend gegen giftige Dämpfe durch Lack oder vor unkontrollierten Bewegungen geschützt ist. Dabei sollte der Betreiber besonders die Erfahrungen und das vorhandene Fachwissen des Bedieners beachten. Denn ein Bediener führt Instandhaltungsarbeiten seltener und eventuell weniger routiniert wie ein Instandhalter durch, dadurch ist das Gefahrenpotential prinzipiell erhöht. Selbstverständlich muss der Betreiber auch die Gefahren für speziell ausgebildetes Instandhaltungspersonal einschätzen, bewerten und ggf. sichere Arbeitsprozeduren einführen.
2. Die Risikobeurteilung
Dass eine Maschine möglichst sicher gestaltet sein sollte, haben wir bereits in vorherigen Blog-Artikeln ausreichend erläutert. Wie Hersteller mittels einer gut durchgeführten Risikobeurteilung zu einer sicheren Maschine gelangen ebenfalls. Ein wesentlicher Punkt einer guten Risikobeurteilung ist die Betrachtung aller Lebensphasen, also auch der Instandhaltung. Wenn der Hersteller schon in der Betriebsanleitung aufgrund seiner Risikobeurteilung auf Gefahren bei der Verwendung des Lösungsmittels hinweist und im Anhang das entsprechende Sicherheitsdatenblatt mitliefert, können Hersteller und Betreiber zum Schutz der Bediener und Instandhalter Hand in Hand zusammenarbeiten. Der Betreiber erfährt, dass sich der Bediener durch Atemschutzmasken und Schutzhandschuhen vor den Gefahren des Lösungsmittels schützen kann und übernimmt diese Informationen in die Betriebsanweisungen für das Personal.
3. Der gesicherte Arbeitsbereich
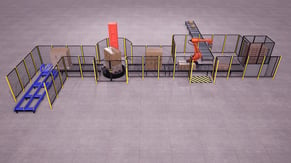
Plötzliche Bewegungen von Maschinenkomponenten können dem Instandhalter das Leben kosten. Schon manch ein Angestellter fand ein trauriges Lebensende unter Hebevorrichtungen, die sich plötzlich absenkten oder unter herabfallenden Roboterarmen. Eine Tragödie für die Angehörigen und oft ein Skandal mit finanziellem Ausmaß für Betreiber und Hersteller. Für eine sichere Wartung gibt es das sogenannte LoTo-Prinzip (Lock Out Tag Out). Mittels LoTo wird ein Weg zum sicheren Trennen von Energiequellen gesucht und definiert. Dazu müssen die gefährlichen Energiequellen in allen Lebensphasen zunächst identifiziert werden. Sobald diese feststehen wird die dauerhafte Abschaltung der Energien durch geeignete Hilfsmittel wie Vorhängeschlösser an Ventilen gewährleistet. Das komplette Prinzip mit allen Abläufen wird im LoTo-Handbuch dokumentiert und allen beteiligten vorgestellt. Praktische Übungen führen zum sicheren Umgang.
4. Das richtige Arbeitsmittel
Die Wirksamkeit von Schutzeinrichtungen muss regelmäßig geprüft werden. Dies regelt schon alleine die Arbeitsmittelbenutzungsrichtlinie. Auch berührungslos wirkende Schutzeinrichtungen wie Lichtschranken, Lichtgitter oder Lichtvorhänge fallen darunter. Denn nur intakte Schutzeinrichtungen können gefahrbringende Bewegungen schnell und zuverlässig stoppen und somit den Bediener und anderes Personal schützen. Der Betreiber hat darauf zu achten, dass diese Wartung regelmäßig durchgeführt und mangelhafte Bauteile ausgetauscht werden. Auch die benötigte persönliche Schutzausrüstung (PSA) muss der Betreiber zur Verfügung stellen. Dies gilt ganz besonders für das Wartungspersonal. Denn das Wartungspersonal wird aufgrund der Arbeiten öfter mit gesundheitsgefährden Stoffen oder heißen Komponenten konfrontiert sein. Welche PSA bei welcher Tätigkeit zu tragen ist und welche Werkzeuge für die Durchführung der Arbeiten benötigt werden, ist sowohl in der Betriebsanleitung der Maschine als auch im LoTo-Konzept beschrieben.
5. Risikofaktor Mensch
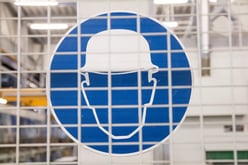
Zu guter Letzt ist das schwächste Glied der Kette zu betrachten: Der Mensch. Die besten Arbeitsanweisungen können dem Instandhalter nicht helfen, wenn er sie nicht einhält. Ignoriert das Personal die Aufforderung, einen Sicherheitshelm zu tragen oder einen Gehörschutz zu benutzen, oder werden ganze Arbeitsschritte zur Sicherung der Maschine aus Zeitgründen weggelassen, kann das schwerwiegende Folgen haben. Um so wichtiger ist die sichere Konstruktion der Maschine. Wenn ein Sicherheitsbereich nur betreten werden kann, sobald die Maschine ausgeschaltet ist, sind viele Risikofaktoren bei Instandhaltungsarbeiten schon vermieden. Weiterhin muss der Betreiber seine Mitarbeiter stets überwachen und auf die Einhaltung der Regeln achten – auch durch Einräumen von ausreichend Zeit für die Wartung. Regelmäßige Schulungen des Personals und Überprüfung der Instandhaltungsarbeiten sind wichtige Bestandteile für einen sicheren Umgang – auch außerhalb des Normalbetriebs.
Damit Sie wissen wie Sie Ihre Risikobeurteilung richtig erstellen, legen wir Ihnen darüber hinaus noch wärmstens unseren Whitepaper „Risikobeurteilung - Fluch & Segen“ ans Herz.
Wenn Sie mehr über die Technische Dokumentation, die CE-Kennzeichnung und die Risikobeurteilung erfahren wollen empfehlen wir Ihnen darüber hinaus unseren Blog-Newsletter.